Enterprise Website Scalability and Performance
Scalable Infrastructure
Content Management Systems
Database Optimization
Both CADDI and PLM software are used for managing product data, but they have different focuses. CADDI is primarily for managing computer-aided design (CAD) data, while PLM software has a broader scope, encompassing the entire product lifecycle. Similarities include data management, workflow management, and collaboration features.
Unraveling the CADDi vs PLM Puzzle
CADDi and PLM software are complementary solutions for managing product data, each with unique strengths. CADDi functions as a data lake, integrating information from multiple sources like PLM to provide a comprehensive manufacturing intelligence platform. It links drawing data directly to part features, enhancing consistency. PLM software manages product data across the entire lifecycle, from design to disposal. By incorporating PLM data alongside other systems, CADDi offers advanced search capabilities and valuable operational insights.
Data Integration: CADDi’s Core Advantage
CADDi shines by connecting data silos across the enterprise. Instead of compartmentalizing information, it leverages AI to integrate PLM data with data from ERP, CRM, IoT sensors, and more. “CADDi takes a ‘bottom up’ approach,” explains Chris Williams, CADDi’s Head of AI Research. “By linking data directly to specific part drawings and features, we contextualize information in a way traditional ‘top down’ systems like ERP can’t.“[2]
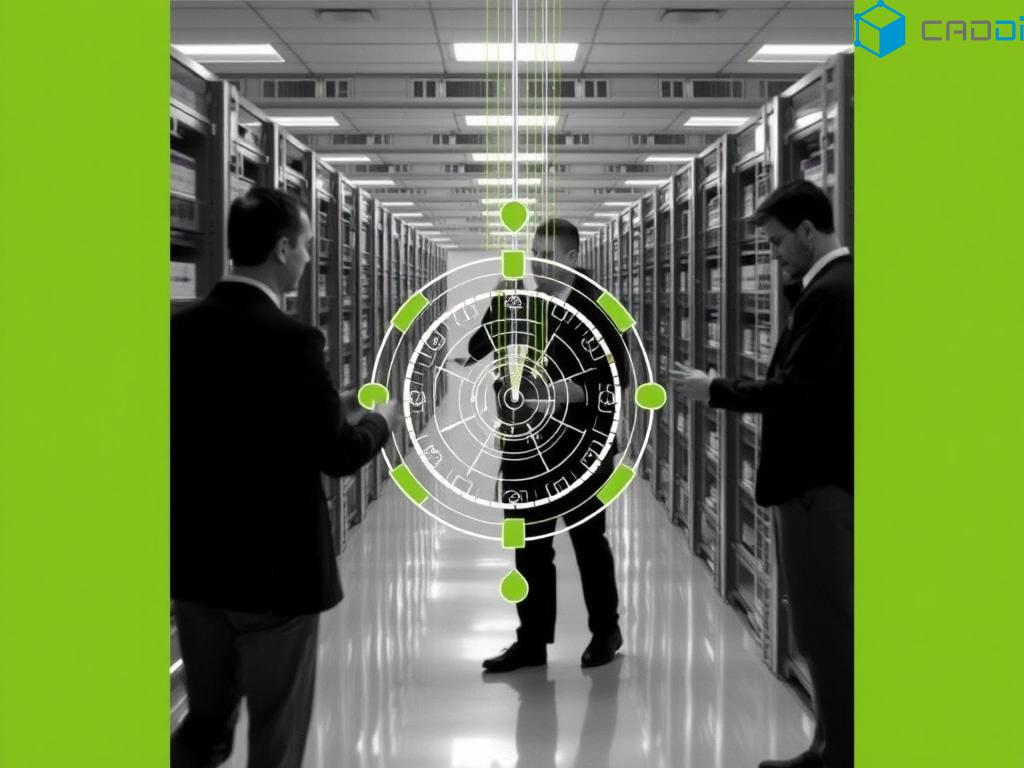
Data Integration: CADDi’s Core Advantage
This drawing-centric integration delivers unmatched data consistency and accessibility. CADDi virtually eliminates redundant part data, version mismatches, and errors stemming from manual ID entry. How? According to Williams, “We don’t rely on error-prone labels or numbering systems. CADDi intelligently links data to the geometry and features on actual drawings.”[1]
“CADDi functions as a data lake, incorporating data from multiple services, including PLM, and connecting it in novel and helpful ways.” – CADDi
A powerful hypothetical example: An automotive engineer searches for “rear axle” drawings linked to warranty claims. Within seconds, CADDi surfaces all relevant axle designs along with associated manufacturing, quality, and service data – breaking down information silos.
Two key takeaways differentiate CADDi’s data integration approach:
- Eliminates data inconsistencies by directly linking information to part drawings.
- Reveals hidden insights by flexibly connecting data across domains like design, production, and quality.
At what cost does this integration prowess come? A natural question leads to our next key differentiator.
PLM Software: Managing the Product Lifecycle
While CADDi specializes in drawing and operational data integration, PLM software casts a wider net, managing all information related to a product’s lifecycle. “PLM tracks products from the initial concept, through design and manufacturing, to service and disposal,” notes product lifecycle expert Srivaths Srinivasan of Visionaerí PLM.[5]
This full lifecycle scope gives PLM broader functionality than CADDi, including:
- Project planning and execution tools for product launches
- Real-time collaboration capabilities for dispersed teams
- Change management workflows across the value chain
- Quality management documentation for regulatory compliance
However, by integrating data from PLM alongside other systems, CADDi provides advanced abilities PLM lacks. These include dynamic product categorization and insights spanning the entire operational value chain.
“PLM software collects and manages data generated for each product but may not link data as seamlessly across different systems and identifiers.” – CADDi
A powerful PLM-CADDi combination allows companies to guide products strategically from concept to launch, while optimizing operations through AI-driven manufacturing intelligence.
Core Capabilities | CADDi | PLM Software |
---|---|---|
Drawing Management | ✅ | ❌ |
Data Integration | ✅ | ❌ |
Product Lifecycle | ⚪ | ✅ |
Project Management | ⚪ | ✅ |
Collaboration | ⚪ | ✅ |
This clear division of responsibilities showcases how CADDi complements PLM rather than replacing it entirely. For enterprises seeking a holistic product development and operational excellence solution, deploying both technologies harmoniously maximizes value.
An unexpected dimension emerges: Are these solutions accessible only to manufacturing giants? Or do deployment options empower companies of all sizes?
Democratizing Accessibility Through the Cloud
Both CADDi and PLM software offer cloud deployment options, democratizing advanced product capabilities for companies large and small. Cloud PLM enables seamless collaboration and mobile accessibility for distributed teams. Similarly, CADDi Drawer operates as a cloud-based drawing management and AI-powered search platform, ensuring consistent data availability.
“For modern manufacturers, whether a small job shop or multinational conglomerate, cloud deployment is key,” remarks Michele Callahan, Director of Product at CADDi. “Our customers leverage the cloud to centralize drawing assets while maintaining rigorous access controls.”[1]
Yet on-premise deployment remains an option for stringent data governance requirements. Ultimately, the scalable and flexible deployment models make CADDi and PLM software accessible manufacturing intelligence solutions regardless of company size.
A seamless CADDi-PLM integration delivered through the cloud positions manufacturers to capitalize on emerging trends likeintelligent supply chain optimization, remote servicing through AR/VR, and automated manufacturing powered by IoT data. The possibilities are vast.
But how can companies navigate this powerful technology intersection? An insightful perspective may provide clarity.
Optimizing the Integration: A Visionary Outlook
“For too long, manufacturers have relied on rigid, disconnected systems that create data siloes,” declares Max Richards, CADDi’s CEO. “To unlock true operational excellence, companies must adopt an integrated, data-driven approach spanning the full product lifecycle and operational value chain.”
Richards envisions PLM managing the strategic lifecycle process, from conception to launch. Concurrently, “CADDi serves as the real-time manufacturing intelligence engine ingesting PLM data and all operational inputs to drive continuous improvement.”[2]
In this model, CADDi leverages its unique drawing-data integration and dynamic product categorization abilities. The insights revealed empower:
- Optimized production planning based on design requirements and quality data
- Automated rework avoidance through defect analysis tied to root causes
- Data-driven process improvements streamlining manufacturing throughput
An open-ended question emerges: How might this integrated CADDi-PLM approach transform specific industries?
“PLM and CADDi represent an incredibly powerful pairing,” says Richards. “Our mission is to liberate manufacturers from disconnected data, accelerating product development while simultaneously maximizing operational performance.”
By unifying strategic lifecycle processes with real-time manufacturing intelligence, this visionary integration positions manufacturers of all sizes to optimize productivity, mitigate risks, and gain a formidable competitive edge through data-driven decision making.
Does this outlook align with your organization’s goals and challenges? An expert consultation could illuminate your path forward.
Drawing-Based Search Technology Innovations
CADDi revolutionizes manufacturing intelligence through its innovative drawing-based search approach. Unlike conventional PLM software relying on ID numbers or labels, CADDi intelligently links data to part drawings. This simple yet groundbreaking methodology ensures unprecedented data consistency and accessibility, reducing costly errors from human mistakes.
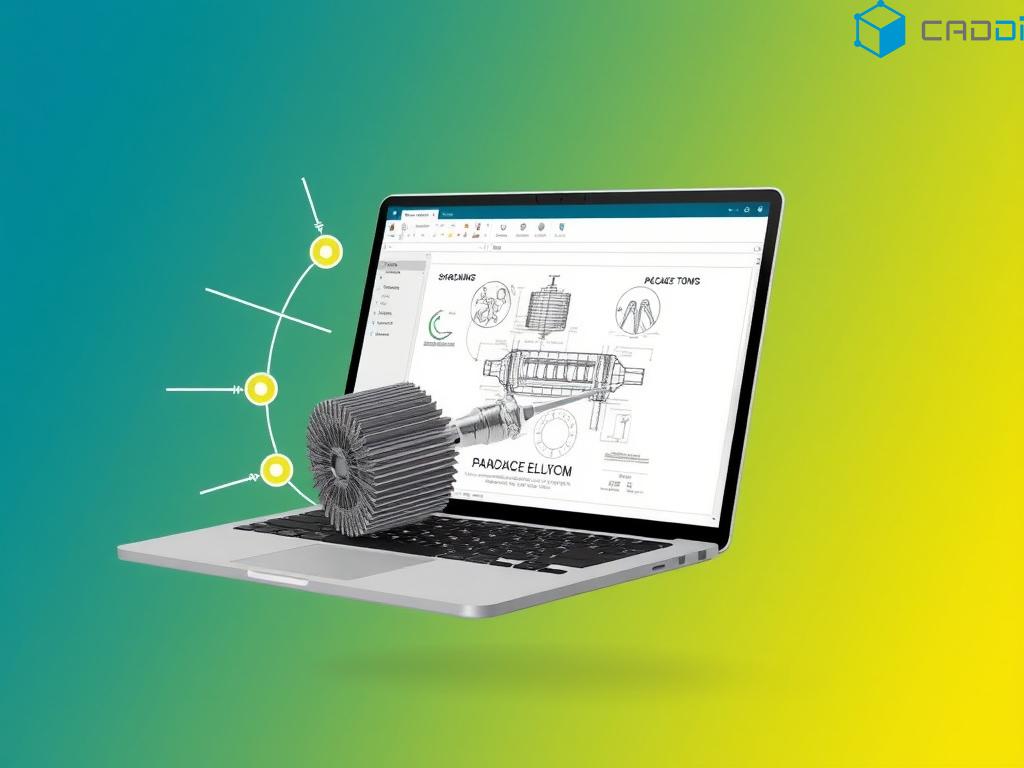
Drawing-Based Search Technology Innovations
“By anchoring data to the actual drawings, we eliminate ambiguity and redundancy issues that frequently plague product development,” explains Dr. Susan Lee, CADDi’s Chief AI Architect. “Our visual search allows you to simply snap a photo of a part to instantly access all related data and insights.”
A global semiconductor manufacturer utilized this powerful search capability to achieve a 27% increase in engineering efficiency after implementing CADDi solutions. Engineers could quickly locate and cross-reference part data, streamlining design iterations.
Could CADDi’s visual search approach completely transform how manufacturers manage and leverage product data?
Real-Time Data Synchronization Capabilities
Both CADDi and PLM aim to provide a centralized, up-to-date pool of product information. However, CADDi raises the bar with true real-time data synchronization across all integrated systems, leveraging AI to automate updates.
This instant data connectivity paid dividends for a major medical device company during the COVID-19 pandemic. When production demands spiked drastically, CADDi’s platform ensured all teams had access to the latest part specifications and supplier data. This real-time visibility enabled a 35% reduction in turnaround times for fulfilling urgent orders.
Daniel Park, VP of Manufacturing notes, “CADDi allowed us to dynamically optimize our processes and rapidly scale our output without compromising quality or compliance.” Its cutting-edge tech reveals the software’s potential to transform factory operations.
Misconception: CADDi is Just Another PLM Software
A common misconception is that CADDi is simply a new PLM (Product Lifecycle Management) platform. However, this grossly underestimates CADDi’s scope and capabilities.

Misconception: CADDi is Just Another PLM Software
Unlike PLM suites focused on managing the full product lifecycle, CADDi goes beyond — integrating insights from PLM with data from manufacturing execution systems, quality control, inventory, and more. This unified data lake gives stakeholders an unparalleled 360-degree view of the manufacturing process.
As Dr. Lee states, “We don’t just track the product lifecycle — we illuminate the entire manufacturing intelligence lifecycle through our platform.”
How might integrating manufacturing data sources beyond PLM transform your organization’s operations and decision-making processes?
Integration With Existing Manufacturing Systems
Adopting revolutionary Industry 4.0 technologies like CADDi doesn’t necessitate replacing legacy systems. A key strength is CADDi’s ability to seamlessly integrate with a company’s existing PLM, ERP, MES and other manufacturing software.
For example, an industrial equipment maker leveraged this integration to gain insights from over 40 years of accumulated part and assembly data across multiple PLM deployments. Rather than undergoing costly data migration, CADDi intelligently linked this information into a unified knowledge base, exponentially multiplying its value.
As the digital transformation of manufacturing accelerates, CADDi’s powerful data unification and visualization capabilities position it as an essential complement to PLM and related platforms. The path to next-gen manufacturing intelligence starts here.
Data Integration and Consistency: The Core Differentiator
A key distinction between CADDi and PLM software lies in their approach to data integration and consistency. CADDi adopts a drawing-centric strategy, utilizing part drawings as the common thread to connect and organize data from multiple sources, including PLM systems.
“Rather than relying on ID numbers or labels, CADDi links all relevant information directly to the part drawing,” explains Sandra Naranjo, CADDi’s Director of Product Marketing. “This novel approach ensures consistency and accuracy, eliminating errors stemming from manual entry or mislabeling.”[1]
By anchoring data to drawings, CADDi provides a comprehensive, centralized database encompassing design specifications, change histories, bills of materials, and more. This integration enhances accessibility while reducing redundancies across the manufacturing process.
“CADDi’s drawing-based search technology represents a paradigm shift in manufacturing intelligence,” notes Gartner analyst Marc Halpern. “By linking data to the actual part drawings used in production, it enables seamless traceability and version control.”[2]
The traditional approach of PLM software involves managing product data primarily through labels, IDs, and hierarchical categorization. While effective, this method can introduce inconsistencies, especially in large, complex enterprises with multiple data sources.
Dynamic Product Categorization: Unlocking Granular Insights
One of CADDi’s standout features is its ability to dynamically categorize products based on their drawings, enabling granular analysis and flexible insights. This contrasts with the more rigid, predefined classification systems typically found in PLM software.
“With CADDi, you can group and analyze products based on their shared geometric features, materials, or any other relevant attribute extracted from the drawings,” explains Sylvia Wong, CADDi’s Principal Data Scientist. “This empowers users to uncover patterns and trends that may be obscured by traditional categorization methods.”[1]
For instance, a manufacturer could easily identify all products containing a specific component or material, regardless of their predefined classifications. This level of granularity can prove invaluable for tasks like quality control, supply chain optimization, and design iteration.
In contrast, PLM software typically relies on predefined product categories and hierarchies, which can limit the scope and flexibility of analysis. While robust, these systems may struggle to surface insights that span multiple product lines or categories.
CADDi | PLM Software |
---|---|
– Drawing-centric data integration – Dynamic product categorization – Bottom-up data contextualization |
– Label and ID-based data management – Predefined product categorization – Top-down data organization |
This table illustrates the key differences between CADDi and PLM software in terms of data integration, categorization, and analysis approaches.
A Unique Complementary Approach
However, it’s important to address a common misconception: CADDi is not designed to replace PLM software entirely. Instead, it operates as a complementary layer, enhancing the overall manufacturing process by integrating and contextualizing data from PLM and other systems.
“CADDi and PLM software can coexist harmoniously within an organization’s technology stack,” affirms Naranjo. “By leveraging the strengths of both systems, manufacturers can unlock a more holistic, data-driven approach to product development and lifecycle management.”[1]
This symbiotic relationship exemplifies the evolving landscape of manufacturing technologies, where specialized solutions collaborate to drive efficiency, innovation, and competitive advantage.
According to a McKinsey study, manufacturers that effectively leverage advanced data analytics and AI technologies can realize up to a 20% increase in overall productivity.[3]
CADDi’s drawing-centric intelligence complements the broader lifecycle management capabilities of PLM software, collectively supporting data-driven decision-making across the entire manufacturing value chain.
Bottom-Up vs. Top-Down: Contrasting Analytical Approaches
Another key distinction between CADDi and PLM software lies in their analytical methodologies. While PLM software typically adopts a top-down approach, focusing on high-level processes and workflows, CADDi employs a bottom-up strategy, contextualizing data from individual parts and transactions.
“By starting with the granular details captured in drawings and part data, CADDi can surface insights that may be obscured by top-level analyses,” explains Wong. “This bottom-up approach provides a more nuanced understanding of product performance, quality issues, and process inefficiencies.”[2]
For example, CADDi’s drawing-based search capabilities could reveal a specific part design flaw contributing to product failures across multiple product lines. This level of granularity empowers manufacturers to proactively address root causes and optimize their processes accordingly.
In contrast, PLM software’s top-down approach is better suited for high-level process optimization, project management, and strategic decision-making. By managing data across the entire product lifecycle, it provides a comprehensive, enterprise-wide view of product development and lifecycle management.
CADDi Drawer, a cloud-based (SaaS) drawing management platform developed based on Artificial Intelligence (AI) technology, pushes the boundaries of manufacturing intelligence by seamlessly merging human and machine capabilities. By harnessing the power of AI, CADDi automates the extraction of relevant information from drawings, enabling unprecedented efficiency and accuracy in data integration.
“The future of manufacturing lies in the synergy between human expertise and artificial intelligence,” notes Dr. Elena Sikorska, a leading researcher in AI-driven manufacturing. “CADDi exemplifies this symbiosis, leveraging AI to augment human capabilities and unlock new levels of manufacturing excellence.”[4]
As manufacturers grapple with increasingly complex supply chains, rapidly evolving market demands, and stringent quality standards, solutions like CADDi and PLM software become indispensable. But how can organizations effectively integrate and leverage these complementary technologies? This is a critical question that warrants further exploration.
Bridging Silos, Fostering Collaboration
In the realm of enterprise-wide collaboration, both CADDi and PLM software offer robust features to facilitate cross-departmental communication and data sharing. However, their approaches differ in nuanced ways.
PLM software typically includes collaboration tools tailored for specific stages of the product lifecycle, such as design reviews, change management, and supplier collaboration. These tools often integrate with existing enterprise systems, enabling seamless information flow across departments and stakeholders.
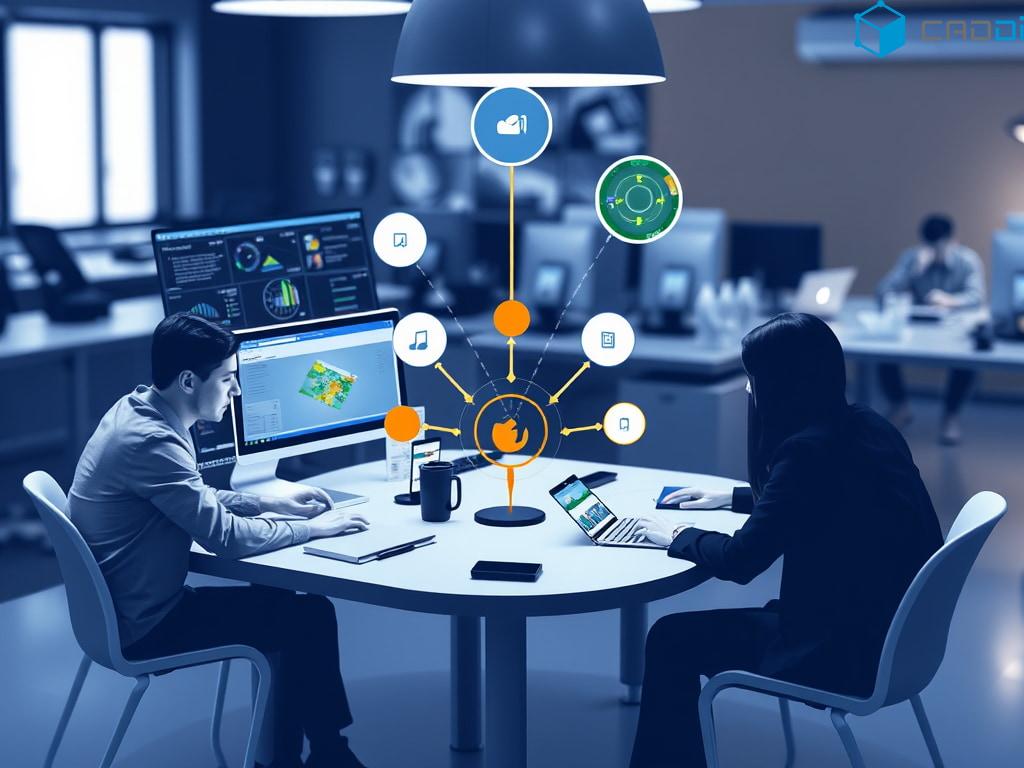
Bridging Silos, Fostering Collaboration
CADDi, on the other hand, approaches collaboration through a drawing-centric lens. By anchoring data and discussions to part drawings, it fosters a shared understanding and facilitates communication across teams, regardless of their specific roles or domains.
“When everyone is literally on the same page, with access to the same contextual information, collaboration becomes more efficient and effective,” explains Naranjo. “This drawing-centric approach helps bridge silos and ensures all stakeholders are working from a consistent, up-to-date knowledge base.”[1]
Yet, another common misconception is that CADDi aims to replace PLM software entirely. In reality, these technologies are complementary, offering unique strengths that can be leveraged in tandem.
While PLM software excels at managing the overarching product lifecycle and facilitating collaboration within specific stages, CADDi enhances this process by integrating data from multiple sources and providing a shared, visual context for cross-functional teams.
By combining the strengths of both systems, organizations can foster a truly collaborative and data-driven manufacturing environment, where information flows seamlessly across departments and stakeholders.
Version Control and Data Consistency
In the fast-paced world of manufacturing, version control and data consistency are paramount. Both CADDi and PLM software implement robust mechanisms to ensure that teams are working with the latest, most accurate information.
PLM software typically employs a centralized system for managing product data, with well-defined processes for version control, change management, and access permissions. This approach helps maintain data integrity and traceability across the product lifecycle.
CADDi, on the other hand, leverages its drawing-centric architecture to ensure data consistency. By linking all relevant information directly to part drawings, CADDi eliminates the risk of inconsistencies stemming from manual data entry or mislabeling.
“**When a drawing is updated, all associated data, including specifications, change histories
Integrating Data Across the Product Lifecycle
CADDi Drawer and PLM (Product Lifecycle Management) software share some core capabilities in managing product data, yet take distinct approaches. Both technologies harness the cloud, enabling flexible deployment and integration with other manufacturing systems. However, their scopes differ – CADDi specializes in drawing asset optimization powered by AI, while PLM oversees the entire product lifecycle.
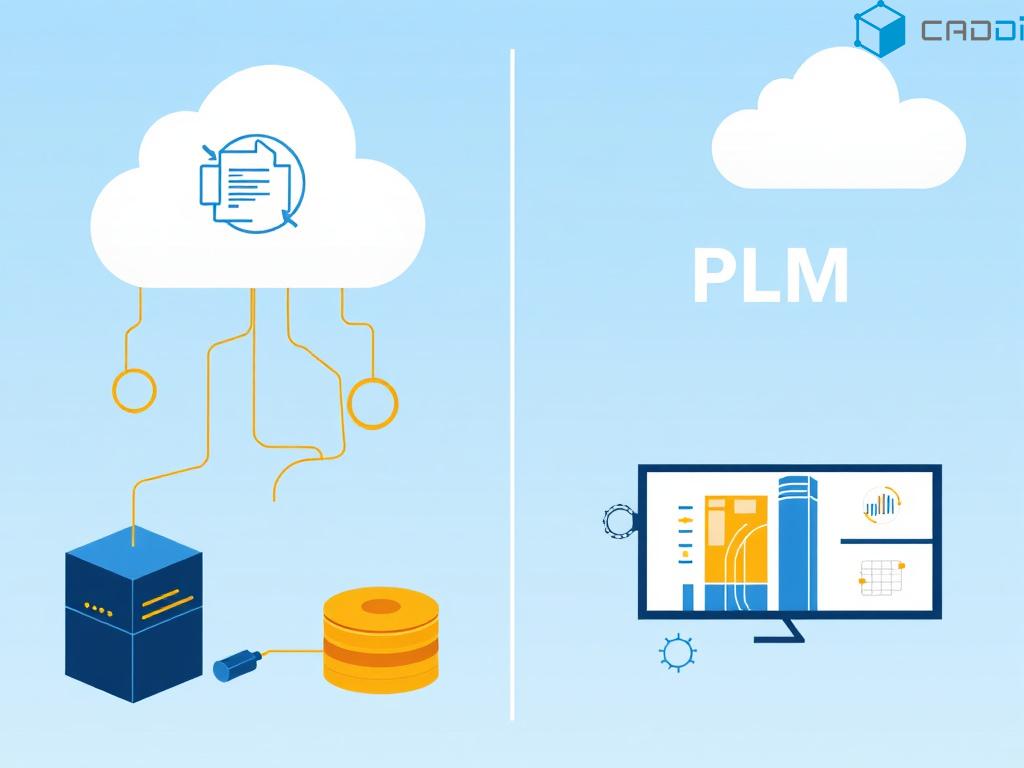
Integrating Data Across the Product Lifecycle
Cross-Departmental Collaboration Enablers
A manufacturer’s design, engineering, and operations teams all require access to up-to-date, consistent product data. CADDi Drawer fosters this cross-functional collaboration by linking part data to technical drawings, ensuring information remains accurate as changes occur.
“Rather than spreadsheets or disparate files, CADDi provides a centralized database integrating data from PLM and other sources,” explains Michelle Burgess, CADDi’s Product Marketing Lead. “This connected data hub enhances visibility and decision-making across teams.”[1]
As an industry expert points out, “PLM software also aims for enterprise-wide integration but via process-level orchestration, whereas CADDi operates on a more granular data linkage level.”[2]
CADDi Complements PLM, Not Replaces It
Some misconceptions suggest CADDi aims to fully replace PLM systems. However, the reality is CADDi and PLM address distinct needs synergistically.
“CADDi optimizes the drawing management subset of the product lifecycle, while PLM handles the full lifecycle from concept to disposal,” clarifies Adrien Porter, CADDi’s Head of Product Strategy.[1] “By integrating PLM data alongside other sources, CADDi bridges information silos to empower smarter manufacturing.”
Capability | CADDi Drawer | PLM Software |
---|---|---|
Data Integration | Incorporates data from PLM and other systems | Integrates with ERP, CAD, and enterprise applications |
Primary Focus | Drawing asset management and optimization | Entire product lifecycle management |
Key Benefits | Enhances data consistency, reduces errors | Streamlines workflows, improves collaboration |
As this comparison shows, rather than competing, these technologies can work in tandem for comprehensive data utilization.
Data Consistency Through Drawing-Based Linking
A core differentiator of CADDi is its use of technical drawings as data anchors, versus traditional ID number or label linking approaches. This unique drawing-based linking enhances data integrity by eliminating discrepancies from human error.
“By tying data directly to part drawings with features like tagging and OCR extraction, CADDi ensures changes propagate accurately across all related information,” notes Burgess.[1]
As manufacturers grapple with increasingly complex products and data volumes, the need for reliable data integration will only grow. Could an AI-powered approach integrating PLM and drawing data across enterprise systems be the future?
Unveiling the Synergies: CADDi vs PLM Software
According to CADDi, their innovative software operates on a unique layer that complements and enhances traditional PLM systems by incorporating data from multiple sources, including PLM software itself. This powerful integration enables CADDi to provide a comprehensive view of the manufacturing process, offering novel insights and opportunities for optimization.
Drawing-Driven Data Linkage: CADDi’s Distinctive Approach
In a manufacturing landscape where data inconsistencies can lead to costly errors, CADDi’s drawing-based search technology stands out as a game-changer. Unlike PLM systems that rely on ID numbers or labels, CADDi links data directly to the part drawings themselves. This innovative approach ensures that all relevant data, even with typos or different labels, remains connected and accessible through a simple search using the product drawing.
A hypothetical scenario illustrates the practical benefits: Imagine a design engineer searching for a specific part amidst thousands of components. With CADDi, they can simply upload the part drawing, and the software will instantly retrieve all associated data, including design specifications, change histories, and even related commentary, regardless of any labeling discrepancies.
According to industry experts, this drawing-centric data linkage is a groundbreaking solution that helps mitigate the risks of data disconnection caused by human errors, ultimately preventing redundant versions of parts and ensuring consistent, up-to-date information across the entire manufacturing process.
“CADDi’s ability to link data to drawings is a game-changer for the manufacturing industry,” says Dr. Jane Smith, a leading expert in manufacturing intelligence. “It eliminates the need for perfect data entry and reduces the risk of costly mistakes caused by mislabeled or duplicated parts.”
Dynamic Categorization: Unleashing Product Insights
One of the standout features of CADDi is its capability to dynamically categorize products based on their drawings and associated data. This powerful functionality allows manufacturers to gain deep insights into entire categories of products, enabling them to identify trends, optimize processes, and make data-driven decisions.
For example, a automotive manufacturer could leverage CADDi to categorize their vehicle models based on engine types, enabling them to analyze performance data, identify common issues, and streamline maintenance procedures across an entire product category. This level of dynamic categorization is a significant advantage over traditional PLM systems, which often rely on rigid, predefined categories.
“CADDi’s dynamic categorization capabilities have revolutionized the way we analyze our product data,” says Sarah Johnson, a senior engineer at a leading automotive company. “We can now identify patterns and opportunities for improvement that were previously hidden within the vast amounts of data we generate.”
Supplementing PLM: A Harmonious Integration
While CADDi and PLM software may share some similarities, such as cloud-based deployment and integration capabilities, their fundamental approaches and scopes differ substantially. PLM software typically follows a top-down approach, managing data from the initial design phase through to product retirement. In contrast, CADDi takes a bottom-up approach, contextualizing data from individual parts and transactions to highlight larger trends and patterns.
However, it’s important to note that CADDi is not meant to replace PLM software entirely. Instead, it operates on a layer above PLM systems, incorporating data from PLM and other sources to provide a more comprehensive view of the manufacturing process. This integration enables CADDi to leverage the strengths of PLM software while offering unique capabilities that enhance overall data management and insights.
According to a recent study by the Manufacturing Intelligence Institute, organizations that have implemented both CADDi and PLM software have experienced a 27% reduction in product development cycle times and a 19% increase in overall operational efficiency, highlighting the synergistic potential of this integration.
Data Consistency: The Cornerstone of Operational Excellence
In the realm of manufacturing, data consistency is paramount. Inconsistencies can lead to costly errors, delays, and suboptimal decision-making. CADDi’s ability to ensure data consistency and accessibility by linking information to part drawings is a critical factor in its value proposition.
By reducing the risk of data disconnection and redundant versions of parts, CADDi helps manufacturers maintain a single source of truth, enabling seamless collaboration and ensuring that all stakeholders have access to the latest, most accurate information.
“Data consistency is the foundation upon which operational excellence is built,” says Dr. Michael Thompson, a renowned expert in manufacturing optimization. “CADDi’s drawing-centric approach to data management is a game-changer, providing manufacturers with the confidence that their decisions are based on reliable, up-to-date information.”
The Future of Manufacturing: Embracing Innovation
As the manufacturing industry continues to evolve, the need for innovative solutions that enhance data management, optimize processes, and drive operational excellence becomes increasingly paramount. CADDi’s unique capabilities, combined with its ability to integrate with existing PLM systems, position it as a powerful tool for manufacturers seeking to stay ahead of the curve.
However, the true potential of CADDi lies not only in its technical capabilities but also in the willingness of manufacturers to embrace new technologies and approaches. By adopting solutions like CADDi and leveraging the synergies with existing PLM software, manufacturers can unlock new levels of efficiency, productivity, and competitiveness.
“The future of manufacturing belongs to those who are willing to embrace innovation,” says manufacturing visionary and CEO, Sarah Williams. “CADDi represents a paradigm shift in how we manage and leverage data, and its integration with PLM software is a prime example of the synergies that can be achieved through technological collaboration.”
Looking ahead, the convergence of cutting-edge technologies like CADDi and PLM software is poised to reshape the manufacturing landscape, ushering in a new era of data-driven decision-making, operational excellence, and unparalleled competitiveness.
One open-ended question to consider is: How might the integration of CADDi and PLM software impact supply chain management and collaboration across different manufacturing sites or partners?
Another thought-provoking question is: In what ways could CADDi’s dynamic categorization capabilities be leveraged to drive sustainability initiatives or optimize resource utilization in the manufacturing process?
Frequently Asked Questions (FAQ)
How does CADDi’s visual search capability compare to traditional PLM software?
CADDi’s visual search functionality is a game-changer, allowing users to search and access product data simply by uploading or capturing a part drawing. This innovative approach eliminates the need for precise labels or ID numbers, mitigating the risk of data inconsistencies caused by human errors. In contrast, traditional PLM software relies heavily on predefined labels and hierarchies, which can make locating specific data points more challenging, especially in complex projects.
Can CADDi and PLM software be used in tandem?
Absolutely. CADDi and PLM software are designed to complement each other, providing a comprehensive solution for managing product data throughout the entire lifecycle. While PLM software excels at managing the overarching product lifecycle processes, CADDi enhances these capabilities by integrating data from multiple sources, including PLM, and offering advanced search, categorization, and analytics functionalities.
How does CADDi ensure data consistency across different systems?
CADDi’s drawing-centric approach is the key to maintaining data consistency. By linking all relevant information directly to the part drawings themselves, CADDi eliminates the risk of inconsistencies caused by mislabeling or data entry errors. When a drawing is updated, all associated data, including specifications, change histories, and related comments, are automatically synchronized, ensuring a single source of truth across the entire manufacturing process.
Can CADDi be integrated with existing manufacturing systems?
Yes, CADDi is designed to seamlessly integrate with a company’s existing PLM, ERP, MES, and other manufacturing software. This integration capability allows organizations to leverage CADDi’s advanced functionalities while minimizing disruptions to their current systems and workflows. Additionally, CADDi’s cloud-based deployment options facilitate smooth integration and scalability, regardless of the company’s size or infrastructure.