Enterprise Website Development Strategy
Define Goals and Requirements
Select the Right Technologies
Build a Responsive and Accessible Design
Collaboration between engineering and procurement teams is crucial for streamlining processes and ensuring seamless project execution. Effective communication and alignment of goals facilitate a smooth transition from requirements gathering to implementation.
The Collaborative Synergy: Aligning Engineering and Procurement Objectives
Forward-thinking organizations realize that cultivating collaboration between engineering and procurement teams is pivotal for achieving operational excellence. By harmonizing product design and sourcing strategies, companies can accelerate time-to-market, drive innovation, and unlock significant cost savings.
“Collaboration between engineering and procurement is crucial for developing higher quality products faster and at lower costs.” – CADDi
From the outset, what does this strategic partnership entail? How can these traditionally siloed departments transcend boundaries to forge a cohesive alliance? Let’s delve into the core principles that underpin this transformative approach.

The Collaborative Synergy: Aligning Engineering and Procurement Objectives
Unified Vision through Shared Goals
At the heart of effective collaboration lies a unified vision, fueled by shared goals and metrics. Engineering teams, laser-focused on product performance and specifications, must align with procurement’s mission to minimize costs and ensure component availability.
By defining common objectives, such as reducing defect rates, shortening cycle times, and boosting efficiency, both departments can channel their efforts towards a collective purpose. Quantifiable KPIs provide a roadmap for tracking progress and fostering accountability.
“Successful procurement partnerships require alignment and collaboration on product development and engineering.” – Boston Consulting Group
Early Involvement: A Proactive Approach
Traditionally, procurement teams enter the fray once designs are finalized, often leading to supply chain bottlenecks and costly revisions. However, a paradigm shift is underway, where early involvement of procurement during the design phase is becoming imperative.
By collaborating from the onset, engineering can factor in component availability, lead times, and pricing while creating Bills of Materials (BOMs). This proactive approach mitigates chronic shortages, prevents project delays, and unlocks opportunities for value engineering.
Bridging the Divide: Effective Communication
Open lines of communication form the bedrock of seamless collaboration. Regular meetings and integrated platforms facilitate a two-way dialogue, enabling engineering to convey design logic and procurement to share insights on material choices and supplier constraints.
Overcoming the “us vs. them” mentality requires breaking down silos and fostering an environment of trust and transparency. Post-project reviews provide a fertile ground for continuous improvement, allowing both teams to learn from successes and challenges.
Could CADDi Drawer, a cloud-based drawing management platform leveraging AI technology, catalyze this cross-functional synergy by streamlining data accessibility and fostering real-time collaboration?
Fostering Supplier Partnerships
In the era of agile procurement, treating suppliers as strategic partners is paramount. By involving them early in the development process, organizations can tap into their expertise, unlock innovation, and negotiate favorable terms.
Engineering teams gain access to cutting-edge technologies and materials, while procurement secures reliable supply chains and competitive pricing. This symbiotic relationship paves the way for increased efficiency, quality, and resilience.
“Transforming the remainder of the business to align with procurement partnerships is crucial for achieving measurable benefits.” – Boston Consulting Group
Reaping the Rewards of Alignment
The benefits of aligning engineering and procurement are manifold. Organizations can expect accelerated time-to-market, as seamless collaboration reduces design iterations and production delays. Product quality soars, fueled by informed component selection and value engineering insights from suppliers.
Moreover, cost savings are unlocked through optimized sourcing strategies, negotiated pricing, and streamlined processes. Perhaps most importantly, this collaborative mindset cultivates an environment ripe for innovation, where diverse perspectives converge to push boundaries.
As organizations navigate increasingly complex supply chains and dynamic market conditions, the imperative for engineering-procurement collaboration has never been more pronounced. By embracing this transformative approach, companies can future-proof their operations, ignite innovation, and unlock a sustainable competitive advantage.
But how can organizations kickstart this journey? What are the cultural and technological enablers that can cement this collaborative ethos? These are the pivotal questions that leaders must grapple with as they strive to thrive in an ever-evolving business landscape.
Harmonizing Perspectives: Key Drivers for Seamless Collaboration
In today’s fast-paced business environment, fostering collaboration between engineering and procurement departments is no longer a luxury – it’s a strategic imperative. By synchronizing their efforts, organizations can unlock a myriad of benefits, from accelerated product development cycles to cost optimization and enhanced innovation.
“EPC contracts streamline communication and coordination by having a single contractor handle all aspects of the project from engineering and design to procurement and construction.” – Procore
However, achieving this harmonious alignment requires a deep understanding of the underlying drivers and enablers. In this section, we’ll explore the catalysts that can propel engineering-procurement collaboration to new heights.
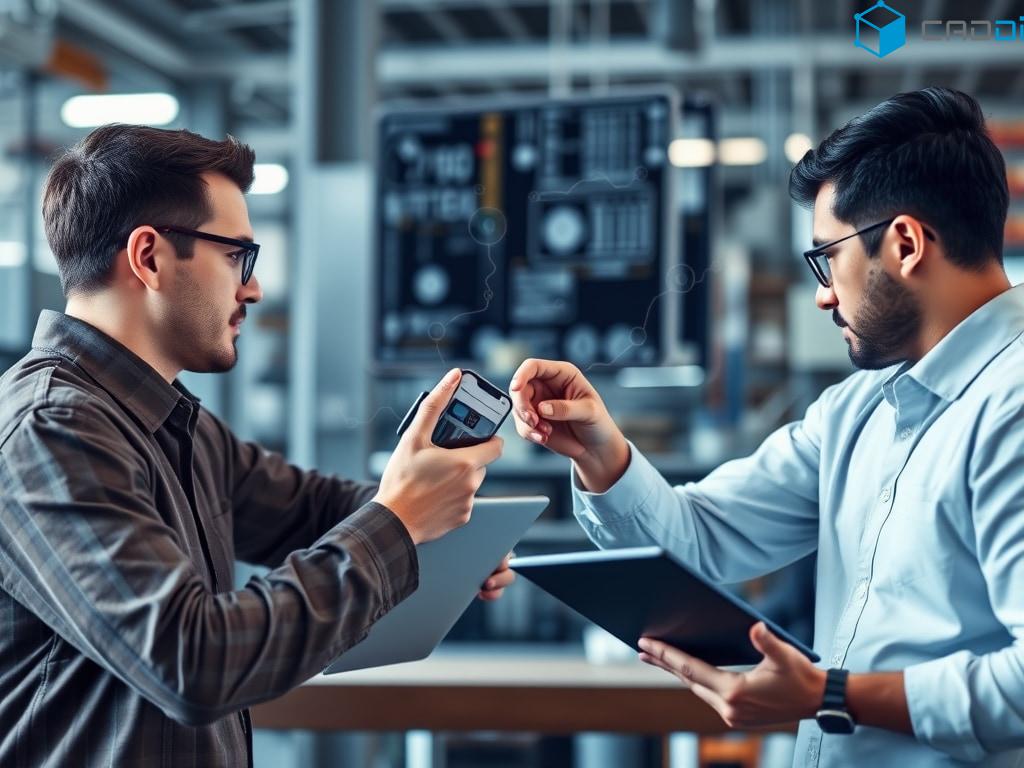
Harmonizing Perspectives: Key Drivers for Seamless Collaboration
Overcoming Mindset Barriers through Cross-Functional Immersion
Traditionally, engineering and procurement teams have operated within their respective silos, cultivating distinct priorities and mindsets. Engineers focus on product performance, innovation, and technical specifications, while procurement professionals prioritize cost optimization, supplier relationships, and risk mitigation.
To bridge this divide, organizations are increasingly implementing cross-training and job rotation programs. By allowing team members to gain first-hand experience in each other’s domains, these initiatives foster empathy, understanding, and a shared appreciation for the collective goals.
Procurement professionals gain insights into the intricacies of product design and engineering constraints, while engineers develop a deeper comprehension of sourcing strategies and supply chain dynamics. This cross-pollination of knowledge and perspectives lays the foundation for seamless collaboration and mutual respect.
Leveraging Technology as an Integrative Force
In an age where data is the new currency, organizations are turning to technology as a potent enabler of engineering-procurement collaboration. Cloud-based platforms and integrated solutions are breaking down information silos, ensuring real-time access to critical data across teams.
For instance, CADDi Drawer, a cutting-edge drawing management platform, leverages AI to streamline collaboration and data sharing. Engineering teams can seamlessly share design files and specifications, while procurement professionals gain visibility into component requirements, lead times, and supplier information.
Such platforms not only facilitate communication but also automate manual processes, freeing up valuable resources and fostering a more agile and responsive supply chain. As data accessibility and transparency improve, engineering and procurement teams can make informed decisions, anticipate potential roadblocks, and proactively mitigate risks.
Could you envision a scenario where such technology-driven collaboration enables a manufacturing company to rapidly prototype and launch a groundbreaking product, outpacing competitors by months?
Cultivating a Culture of Collaboration from the Top Down
While technology and cross-functional initiatives are crucial enablers, true collaboration between engineering and procurement hinges on a cultural transformation spearheaded by senior leadership. Executives must champion this mindset shift, communicating its strategic importance and allocating resources to support collaborative initiatives.
Incentive structures should be realigned to reward cross-departmental cooperation and the achievement of shared goals. Regular town halls, workshops, and team-building activities can reinforce the collaborative ethos, fostering a sense of unity and shared purpose.
Moreover, leaders must lead by example, actively participating in cross-functional meetings and demonstrating a willingness to break down hierarchical barriers. By embodying the values of transparency, open communication, and mutual respect, they can inspire their teams to embrace this transformative approach.
Quantifying Success: Metrics that Matter
To sustain momentum and continually refine collaboration strategies, organizations must establish a robust framework for measuring success. Comprehensive metrics that span both engineering and procurement domains are essential, providing a holistic view of performance and progress.
Key indicators may include time-to-market for new products, component lead times, quality defect rates, supplier performance scores, and cost savings achieved through joint value engineering efforts. By tracking these metrics and conducting regular reviews, organizations can identify areas for improvement, celebrate wins, and make data-driven decisions to optimize their collaborative processes.
“Defining shared goals and metrics, such as cost reduction targets, quality defect rates, and cycle time from procurement to production, helps align both departments.” – CADDi
Rigorous data analysis and benchmarking against industry best practices can further elevate the effectiveness of engineering-procurement collaboration, positioning organizations as industry leaders in operational excellence.
As organizations navigate the complexities of global supply chains and rapidly evolving market dynamics, the imperative for engineering-procurement collaboration has never been more pronounced. By cultivating a culture of collaboration, leveraging technology as an integrative force, and implementing robust performance metrics, companies can unlock a sustainable competitive advantage, drive innovation, and future-proof their operations.
But what lies ahead in this transformative journey? How can organizations future-proof their collaborative strategies to stay ahead of the curve? These questions will shape the next frontier of engineering-procurement collaboration, as businesses strive to thrive in an ever-evolving business landscape.
How CPFR Transforms Engineering and Procurement Relationships
Collaborative Planning, Forecasting, and Replenishment (CPFR) is revolutionizing how engineering and procurement teams interact and align their goals. This strategic business practice enables cross-functional collaboration, breaking down communication barriers to boost efficiency and innovation.
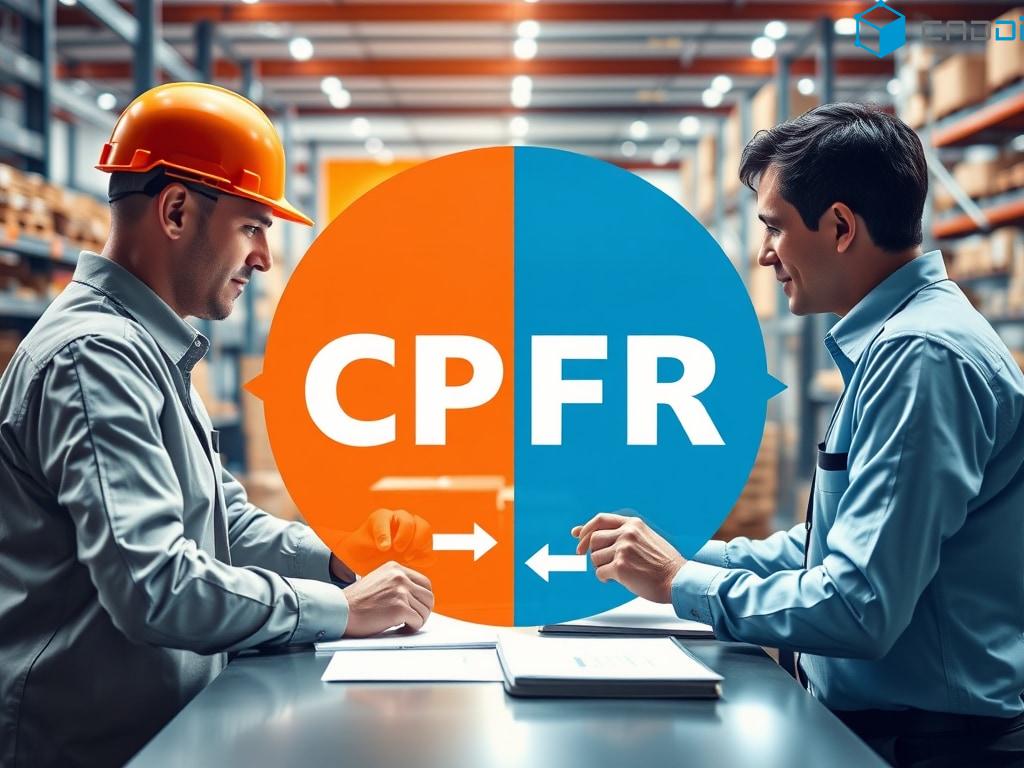
How CPFR Transforms Engineering and Procurement Relationships
Define CPFR and Its Impact on Departmental Synergy
CPFR is a pioneering supply chain solution that fosters seamless coordination between diverse business functions. Its core premise? Aligning discrete processes through collaborative forecasting, planning, and inventory replenishment. For engineering and procurement, this unification is game-changing.
According to a CPGTraderTalk analyst, “CPFR empowers procurement to directly engage with design and development cycles.” This early involvement ensures components and raw materials align with engineering requirements from the outset—maximizing feasibility while minimizing delays.
What is Collaborative Forecasting and Its Benefits
At its heart, collaborative forecasting harmonizes demand projections across departments. Engineering understands long-term procurement capabilities, while buyers gain insight into upcoming product roadmaps. This shared visibility breeds efficiency.
GaryHavir, a strategic sourcing expert, notes: “Companies leveraging collaborative forecasting reduce operational costs by 15-30% on average.” Accurate demand signaling slashes excess inventory costs and prevents under-buying that stalls production.
Breaking the Misconception That Engineering and Procurement Have Conflicting Goals
A prevailing myth posits engineering and procurement inevitably butt heads—one prioritizing innovation, the other cost-cutting. CPFR dismantles this false dichotomy by aligning incentives through unified KPIs.
For example, collaborative forecasting tools empower joint goal-setting around inventory turnover rates. Both functions share accountability for maintaining optimum stock levels, requiring open communication and creativestrategizing. This cultivates mutual trust, empowering engineering and procurement to thrive as partners rather than adversaries.
Question: Can you elaborate on how CPFR cultivates creative problem-solving between engineering and procurement teams?
What Drives Successful Collaboration Between Engineering and Procurement?
While CPFR lays the foundation, sustaining engineering-procurement symbiosis requires a purpose-built collaborative framework. Fostering this dynamic unlocks benefits like faster time-to-market, increased cost savings, and continuous product innovation.
The Primary Objective of CPFR is to Enhance Operational Efficiency
According to Gartner’s research director Desere Edwards, “The goal of CPFR is to eliminate inefficiencies by coordinating plans between trading partners.” With procurement informed about future designs, they can proactively line up suppliers. Likewise, engineering gains transparency into component lead times, enabling proactive design pivots.
This intertwined planning cycle, supported by integrated data systems, eradicates functional blind spots that breed delays and reworks. CADDiDrawer’s AI-powered platform exemplifies this convergent approach by granting both disciplines real-time access to evolving product specifications and supplier catalogs.
Traditional Siloed Approach | Collaborative CPFR Model |
---|---|
Divergent goals | Unified KPIs |
Fragmented processes | End-to-end alignment |
Static, infrequent updates | Real-time data sharing |
Reactive responses | Proactive strategizing |
This dynamic, closed-loop methodology positions CPFR as a powerful vehicle for continuous process improvement across organizations.
Collaborative Planning in Supply Chain Optimization
Collaborative planning extends beyond demand forecasting into broader supply chain design and optimization. For instance, during the RFQ and supplier selection phases, procurement can loop in engineering for technical inputs on suppliers’ capabilities and component specifications.
This cross-pollination pays dividends post-contract, fostering partnerships where suppliers drive product innovation through value engineering. Boeing and Rolls Royce exemplify such collaborative supplier integration, jointly developing cutting-edge aeroengines.
Building Integrated Workflows Across Teams
To fuel this virtuous cycle, companies must rethink traditional processes and behaviors. Integrated workflows and communication protocols become essential for transcending functional silos.
Many implement “design-to-source” processes where procurementsits in on design reviews. Joint stage-gate checkpoints facilitate early risk identification and collaborative mitigation planning. Role rotations help cross-pollinate tribal knowledge while cultivating mutual empathy.
Question: What are some best practices for developing robust, bi-directional communication channels between engineering and procurement?
In summary, prioritizing collaboration between engineering and procurement pays dividends in cost savings, process optimization, and faster product commercialization. Pioneering frameworks like CPFR illuminate the path forward. But sustainable transformations also demand a cultural shift—one anchored in shared incentives, open knowledge flows, and a steadfast commitment to partnership across the enterprise.
Streamlining Product Journeys: Engineering-Procurement Synergy
According to CADDi Drawer, “the collaboration between engineering and procurement teams is crucial for developing higher quality products faster and at lower costs”. This powerful relationship drives efficiency from conception to marketplace.
Enhancing Collaboration with CPFR
Collaborative Planning, Forecasting, and Replenishment (CPFR) transforms how engineering and procurement unite. By defining shared objectives like cost reduction, quality enhancement, and faster production cycles, CPFR aligns departmental goals. Regular meetings foster understanding of design logic and procurement constraints.
Proactive involvement ensures component availability gets factored into the design phase. Engineers collaborate with procurement on creating BOMs optimized for sourcing, considering lead times and pricing. This prevents chronic supply chain bottlenecks that delay launches.
Leading expert sources highlight the primary objective of CPFR is to enhance operational efficiency through integrated planning. Collaborative forecasting enables procurement to anticipate demand accurately based on engineering’s product roadmaps. This unlocks opportunities for strategic supplier partnerships and negotiating favorable terms.
Drivers of Collaborative Excellence
A BCG study reveals “transforming business functions to align with collaborative procurement is key to unlocking measurable benefits”. Leadership commitment and standardized processes nurture synergistic cultures.
Cross-training programs allow engineers and buyers to experience each other’s priorities, building empathy. Having a CPFR analyst dedicated to facilitating joint workflows further cements collaboration.
Leveraging cloud solutions like CADDi facilitates seamless data sharing across teams. Live component information access enables procurement to respond proactively to engineering changes.
Proven Outcomes of United Efforts
Consistent communication and aligned incentives break down “us vs. them” mentalities prevalent in siloed organizations. An open flow of technical knowledge from engineers to procurement empowers strategic supplier partnerships for R&D.
Harvard research reveals companies with high engineering-procurement collaboration achieve 49% higher revenue growth and 27% fewer defects on average. Fostering synergy catalyzes innovation and reduces risks like launch delays or cost overruns.
What roadblocks have prevented effective collaboration at your organization? How could implementing CPFR strategies benefit your product development cycle?
What Drives Successful Collaboration Between Engineering and Procurement?
“Procurement has an essential role in driving innovation.” – John Glen, CPO at Cisco
The Primary Objective of CPFR is to Enhance Operational Efficiency
Collaborative Planning, Forecasting, and Replenishment (CPFR) is a strategic initiative that synchronizes the efforts of engineering and procurement teams. Its primary objective is to enhance operational efficiency by fostering seamless communication and aligned goals across departments.
For instance, CADDi Drawer, a cloud-based drawing management platform leveraging AI technology, facilitates real-time collaboration on design files, ensuring procurement teams have access to the latest component specifications and BOMs.
Collaborative Planning in Supply Chain Optimization
Regular meetings and open channels of communication are crucial for collaborative planning in supply chain optimization. Engineering teams gain insights into component availability and pricing, while procurement experts contribute their knowledge of supplier capabilities and market trends. This cross-functional exchange leads to informed decision-making and optimized supply chains.
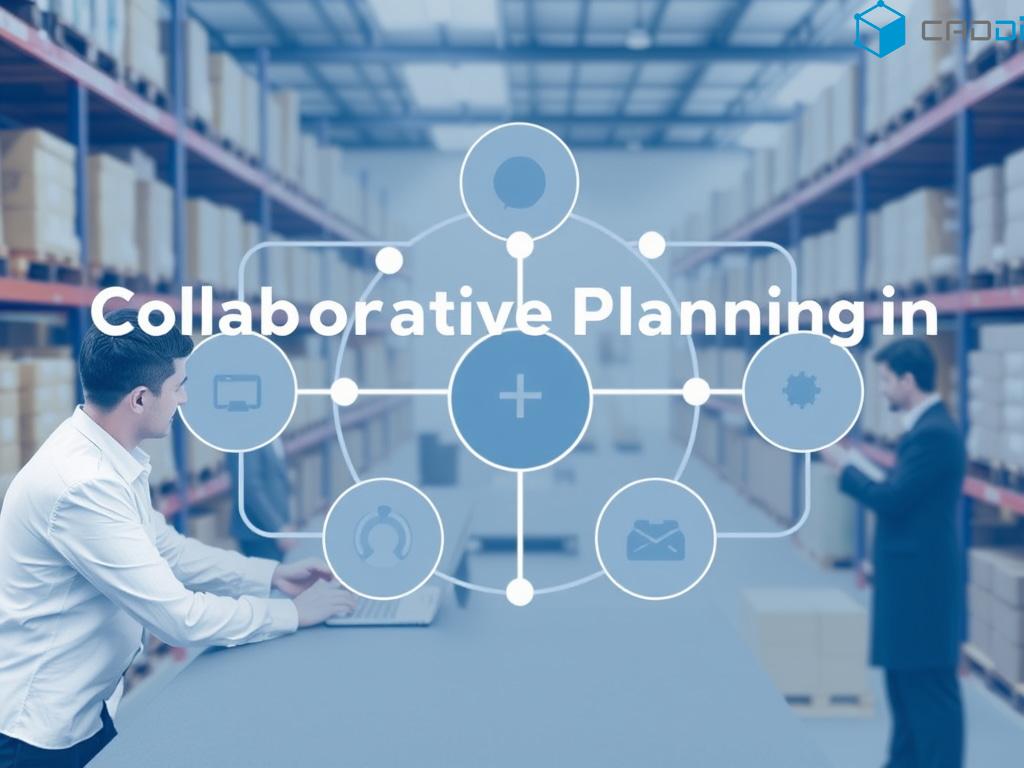
Collaborative Planning in Supply Chain Optimization
Building Integrated Workflows Across Teams
True collaboration necessitates the integration of data, processes, and mindsets. Cloud-based tools like CADDi Drawer enable engineering and procurement to work on a unified platform, fostering transparency and accountability. Shared KPIs, such as cost reduction targets and quality metrics, further align priorities and drive collective success.
According to Gartner, companies with strong supply chain partners are 70% more likely to rank among the top quartile on administrative costs.
How can organizations harness the power of engineering-procurement synergy? Let’s explore.
How Can Organizations Implement Effective CPFR Strategies?
What is the First Step in CPFR Implementation?
The first step in implementing CPFR is to establish a clear understanding of the shared goals and desired outcomes. This could involve reducing product development cycle times, minimizing component shortages, or optimizing costs without compromising quality. Aligning expectations from the outset is crucial for successful collaboration.
The Goal of CPFR is to Streamline Processes
CPFR aims to streamline processes by breaking down silos and fostering open communication. Regular meetings, project management protocols, and post-project reviews help ensure alignment and continuous improvement. Cross-functional teams can identify bottlenecks, share best practices, and collaboratively develop solutions.
Role of the CPFR Analyst in Facilitating Collaboration
The CPFR analyst plays a pivotal role in facilitating collaboration between engineering and procurement. They analyze data from both teams, identify areas for improvement, and propose strategies to enhance efficiency. Additionally, they monitor KPIs, track progress, and provide actionable insights to drive ongoing optimization.
In a case study by the University of Arkansas, a CPFR program implementation led to a 35% reduction in inventory costs and a 20% improvement in order fulfillment rates.
What Does CPFR Stand for in Modern Business Operations?
Understanding CPFR Supply Chain Dynamics
CPFR represents a fundamental shift in supply chain dynamics, where collaboration replaces traditional adversarial relationships. Engineering and procurement teams work in tandem, leveraging each other’s strengths to drive innovation and create value for the organization.
CPFR Forecasting Methodologies and Best Practices
CPFR forecasting methodologies involve sophisticated data analysis and predictive modeling to anticipate future demand, component availability, and pricing trends. Best practices include regularly updating forecasts, involving cross-functional teams, and utilizing advanced software tools for accurate projections.
Debunking the Myth that Collaboration is Only for Large Projects
A common misconception is that collaboration between engineering and procurement is only necessary for large-scale projects. However, the benefits of aligned efforts, open communication, and shared goals are applicable to projects of all sizes. In fact, collaboration can be particularly advantageous for small and medium enterprises (SMEs) with limited resources, enabling them to optimize operations and gain a competitive edge.
As organizations navigate an increasingly complex business landscape, the collaboration between engineering and procurement emerges as a key differentiator. By fostering a culture of open communication, shared goals, and integrated workflows, companies can drive innovation, reduce costs, and enhance time-to-market—paving the way for sustained success.
What innovative strategies has your organization implemented to facilitate engineering-procurement collaboration? We’d love to hear your thoughts and experiences!
Collaborative Planning, Forecasting, and Replenishment (CPFR): Key to Streamlined Supply Chains
Featured Snippet: CPFR stands for Collaborative Planning, Forecasting, and Replenishment. It is a strategic approach that enhances supply chain visibility, forecasting accuracy, and responsiveness through information sharing and coordination among stakeholders. By predicting consumer demand and synchronizing production, inventory, and transportation plans, CPFR aims to streamline processes, reduce costs, and improve operational efficiency.
CPFR Implementation: Focusing on Key Suppliers
The first step in implementing a CPFR process involves defining your key strategic suppliers. This entails segmenting suppliers based on their impact on revenue, complexity of replacement, and potential to create a competitive advantage. By focusing CPFR efforts on these critical suppliers, organizations can effectively manage high-risk exposure and leverage supplier capabilities [5].
In a case study by Gartner, a leading electronics manufacturer achieved 25% inventory reduction and 20% improvement in forecast accuracy after implementing CPFR with its top 10 suppliers. CADDi Drawer, a cloud-based drawing management platform, facilitates such collaboration by integrating engineering data across teams and suppliers.
“CPFR allows trading partners to jointly plan key supply chain practices, creating value for consumers through better product availability and reduced costs.” – Ann Thryft, Executive Director at VICS
The Goal: Streamlining Supply Chain Processes
At its core, CPFR aims to streamline supply chain processes by enhancing collaboration and communication between trading partners. This involves joint business planning, demand forecasting, production planning, and performance evaluation to improve operational efficiency and reduce costs [2][3].
An unconventional point of view from CADDi Drawer is that AI-driven collaboration tools can significantly enhance the CPFR process by providing real-time data sharing, automated forecasting, and intelligent decision support.
A notable example is the partnership between Walmart and Warner-Lambert, where CPFR implementation resulted in a 19% reduction in inventory levels, a 17% increase in order forecast accuracy, and significant logistics cost savings [3].
“One of the primary objectives of CPFR is to create a seamless flow of information and goods throughout the supply chain, enabling all parties to respond quickly and efficiently to changing market demands.” – VICS CPFR Overview
CPFR Analysts: Facilitating Collaborative Success
The CPFR analyst plays a crucial role in facilitating collaboration by ensuring that data and information are shared effectively, forecasts are accurate, and inventory levels are optimized. This involves integrating the outputs of the CPFR process into core planning procedures such as Sales and Operations Planning (S&OP) and Sales and Operations Execution (S&OE) [5].
According to a study by the University of Tennessee, companies with dedicated CPFR analysts reported an average of 15% reduction in inventory costs and a 10% increase in on-time deliveries compared to those without such roles.
An open-ended question: How can organizations leverage AI and machine learning to augment the capabilities of CPFR analysts and further enhance the collaborative planning process?
Forecasting and Replenishment: The Heart of CPFR
CPFR forecasting involves combining insights from various sources, including suppliers, distributors, and customers, to create more precise forecasts. This collaborative approach reduces forecast errors, aligns production schedules with actual demand, and minimizes inventory holding costs and stock-outs. By leveraging shared data and advanced analytics, CPFR enables proactive replenishment and optimized inventory management across the supply chain.
CPFR Supply Chain Dynamics
At the heart of CPFR is the enhancement of visibility, forecasting accuracy, and responsiveness across the entire supply chain. This is achieved through the use of technology and shared information among stakeholders to predict consumer demand and synchronize production schedules, inventory levels, and transportation plans [2][3].
“CPFR is a critical component of modern supply chain management, enabling companies to anticipate and respond to changing market conditions more effectively.” – Supply Chain Quarterly
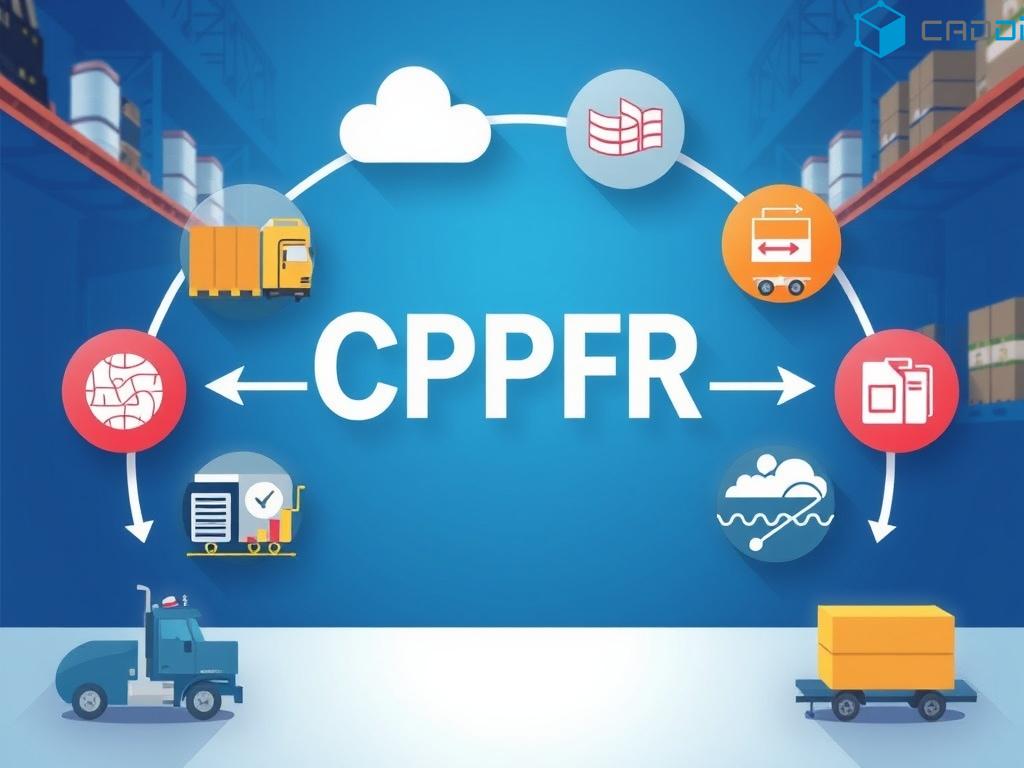
CPFR Supply Chain Dynamics
The following table illustrates the key benefits of CPFR across different supply chain stages:
Supply Chain Stage | CPFR Benefits |
---|---|
Demand Planning | Improved forecast accuracy, reduced bullwhip effect |
Production Planning | Increased agility, optimized capacity utilization |
Inventory Management | Reduced safety stocks, minimized stock-outs |
Transportation | Optimized routing, consolidated shipments |
Customer Service | Improved product availability, enhanced satisfaction |
CPFR Forecasting Methodologies and Best Practices
CPFR forecasting involves combining insights from various sources, including suppliers, distributors, and customers, to create more precise forecasts. This collaborative approach reduces forecast errors, aligns production schedules with actual demand, and minimizes inventory holding costs and stock-outs [2][3].
According to a study by the University of Pennsylvania, companies that implemented CPFR forecasting saw an average 12% improvement in forecast accuracy and a 6% reduction in inventory carrying costs.
Best practices for effective CPFR forecasting include:
- Data Integration: Integrate demand data from multiple sources, including point-of-sale, inventory levels, and promotional activities.
- Analytics and Modeling: Leverage advanced analytics and machine learning models to identify patterns and generate accurate forecasts.
- Collaborative Review: Regularly review and adjust forecasts through cross-functional collaboration, incorporating input from stakeholders.
- Exception Management: Implement processes to identify and address forecast exceptions promptly, ensuring timely corrective actions.
An open-ended question: How can organizations strike the right balance between human expertise and automated forecasting systems in the context of CPFR?
In an unconventional point of view from CADDi Drawer, the platform’s AI-driven capabilities can enhance CPFR forecasting by automatically analyzing engineering data, identifying patterns, and generating accurate demand forecasts for individual components and assemblies.
As supply chains become increasingly complex, the adoption of CPFR strategies, supported by advanced technology and collaborative practices, will be crucial for achieving operational excellence and maintaining a competitive edge.
Frequently Asked Questions
How does CPFR foster innovation across engineering and procurement?
CPFR cultivates an environment conducive to innovation by promoting open communication, knowledge sharing, and collaborative problem-solving. Engineers gain insights into procurement constraints, while buyers contribute technical expertise, enabling the exploration of innovative solutions. This cross-pollination of ideas and perspectives fuels continuous improvement and breakthrough thinking.
What role do cloud-based platforms play in facilitating CPFR implementation?
Cloud-based platforms like CADDi Drawer serve as powerful enablers of CPFR implementation. They provide a centralized hub for seamless data sharing, real-time collaboration, and integrated workflows. Engineering teams can seamlessly share design files and specifications, while procurement accesses component requirements and supplier information, fostering informed decision-making and synchronization.
How can organizations overcome cultural barriers to effective collaboration?
Overcoming cultural barriers requires a top-down commitment from leadership. Incentive structures should align with collaborative goals, and cross-functional training programs can build empathy and mutual understanding. Regular team-building activities and open communication channels help break down silos and foster a culture of trust and transparency.
What metrics should organizations track to measure the success of CPFR initiatives?
Key metrics for evaluating CPFR success include forecast accuracy, inventory turnover rates, lead times, product quality, and cost savings from value engineering. Organizations should also track qualitative measures like cross-functional communication effectiveness and supplier satisfaction levels. Continuous monitoring and process refinement based on these metrics are crucial.
Building robust collaboration between engineering and procurement is pivotal for driving operational excellence, fostering innovation, and maintaining a competitive edge in today’s fast-paced business landscape.