Continuous improvement manufacturing refers to the ongoing efforts to enhance processes, eliminate waste, and optimize operations for increased efficiency and quality. It involves identifying and implementing incremental improvements through data-driven analysis and employee engagement.
Embracing the Journey of Relentless Betterment
Continuous improvement in manufacturing embodies an organizational mindset striving for perpetual enhancement. It drives companies to identify opportunities, implement impactful changes, and sustain progress through meticulous data analysis and stakeholder engagement[4]. This unwavering pursuit of excellence optimizes processes, enhances quality, and ultimately bolsters competitive advantage[1].
“Continuous improvement is more than a mere strategy; it’s a transformative culture that permeates every aspect of an organization.” – Joseph M. Juran, Quality Management Pioneer
Continuous Improvement in Manufacturing
Continuous Improvement is the subject, representing the ongoing efforts to enhance manufacturing operations.
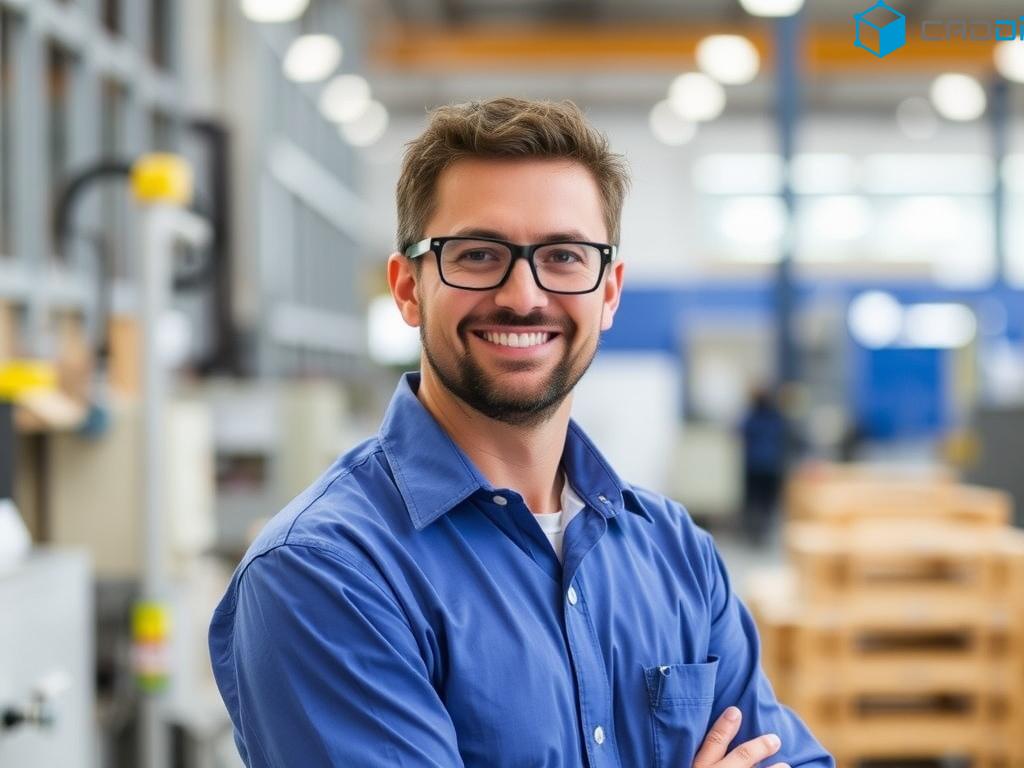
Continuous Improvement in Manufacturing
The predicate encompasses five crucial actions:
- Identify and Analyze: Pinpoint areas for improvement and gather data to establish a performance baseline[3][4][5].
- Implement Changes: Execute incremental enhancements or groundbreaking advancements to refine processes, products, or services[1][2][5].
- Measure Outcomes: Collect and analyze data to quantify the impact of improvements and assess their effectiveness[3][4][5].
- Involve Stakeholders: Engage employees, customers, and leadership to ensure a holistic and sustainable approach[2][3][5].
- Sustain Improvements: Implement controls and monitoring to maintain enhancements over the long term[1][4][5].
- The object involves five target results:
- Efficient Production: Achieve streamlined processes with minimal waste, unplanned interruptions, and unnecessary actions[3][4][5].
- Quality Enhancement: Improve product quality, safety, and customer satisfaction through continuous refinement[1][2][5].
- Operational Excellence: Foster a culture of excellence, adapting to evolving regulations and market conditions[2][3][5].
- Cost Reduction: Minimize expenses by optimizing processes, reducing inventory, and eliminating defects[3][4][5].
- Competitive Advantage: Maintain an edge through innovation, adaptability, and customer-focused operations[2][3][5].
How can manufacturers integrate continuous improvement into their daily operations for sustainable growth?
Frameworks Paving the Path to Perfection
Robust methodologies underpin the journey of continuous improvement, providing structured roadmaps for organizations to follow. Among the most renowned approaches are Lean Manufacturing, Six Sigma, and Total Quality Management (TQM)[1][3][4].
Lean Manufacturing emphasizes the relentless elimination of waste, whether in the form of excess inventory, unnecessary motion, or defective products. By streamlining processes and reducing cycle times, Lean principles empower manufacturers to enhance efficiency and boost productivity[2][3][5].
Six Sigma, with its data-driven decision-making and statistical analysis, targets the reduction of process defects and variations. This rigorous approach enables organizations to improve quality, minimize costs, and ultimately drive customer satisfaction[3].
Total Quality Management (TQM) advocates for a holistic quality culture that permeates every aspect of an organization. By involving all stakeholders, from executives to front-line workers, TQM fosters a collaborative environment where continuous improvement becomes an intrinsic value[1][4].
Methodology | Focus | Key Principles | Impact |
---|---|---|---|
Lean Manufacturing | Waste elimination, process optimization | Just-in-Time, Kaizen, Value Stream Mapping | Increased efficiency, reduced cycle times |
Six Sigma | Defect reduction, variation minimization | DMAIC, Statistical analysis, Root cause analysis | Improved quality, cost savings |
Total Quality Management (TQM) | Holistic quality culture | Employee involvement, Customer focus, Continuous improvement | Enhanced customer satisfaction, organizational excellence |
These methodologies are not mutually exclusive; in fact, many organizations integrate their principles to amplify their continuous improvement efforts[2]. For instance, General Electric has successfully combined Lean practices with Six Sigma to drive operational excellence and efficiency[3].
Empowering a Culture of Improvement
While frameworks provide structure, continuous improvement thrives on the engagement and empowerment of people. Manufacturers must cultivate a learning environment that encourages employee participation, problem-solving, and innovative thinking[2][5].
The success of Harley-Davidson’s continuous improvement initiatives can be attributed to their unwavering focus on involving employees at all levels. By fostering a culture of trust and open communication, the company has enabled its workforce to actively identify opportunities for improvement and implement effective solutions[4].
“Continuous improvement is better thinking put into practice for the betterment of a product, service, or process.” – Bob Parsons, Founder of GoDaddy
Engaging employees not only enhances operational efficiency but also boosts morale and job satisfaction[2][5]. When workers feel valued and empowered, they become invested in the company’s success, creating a virtuous cycle of continuous improvement.
How can organizations strike the right balance between structured methodologies and fostering a culture of employee engagement?
The Catalyst for Data-Driven Improvement
In the era of Industry 4.0, digital technologies have emerged as powerful enablers of continuous improvement in manufacturing. Real-time data and predictive analytics provide unprecedented visibility into production processes, allowing organizations to identify inefficiencies, optimize operations, and make informed decisions[2][5].
PTC, a leading provider of industrial software solutions, reports that their digital manufacturing solutions can increase efficiency by up to 20% while delivering real-time performance data[2]. This data-driven approach empowers manufacturers to continuously refine their processes, reduce waste, and enhance product quality.
Furthermore, digital transformation facilitates the integration of continuous improvement methodologies with emerging technologies like 3D printing, robotics, and artificial intelligence. This convergence opens up new avenues for innovation, enabling manufacturers to rapidly prototype, test, and iterate on product designs, ultimately accelerating their continuous improvement cycles[5].
Beyond operational enhancements, digital technologies also play a crucial role in engaging stakeholders and fostering collaboration. Virtual reality and augmented reality applications can immerse employees in simulated manufacturing environments, providing hands-on training and facilitating knowledge sharing[2].
What innovative digital solutions can manufacturers leverage to unlock the full potential of continuous improvement?
A Perpetual Pursuit of Perfection
Continuous improvement in manufacturing is not a one-time initiative but rather a perpetual journey towards operational excellence. By embracing methodologies like Lean, Six Sigma, and TQM, empowering employees, and harnessing digital technologies, manufacturers can optimize processes, enhance quality, and drive customer satisfaction.
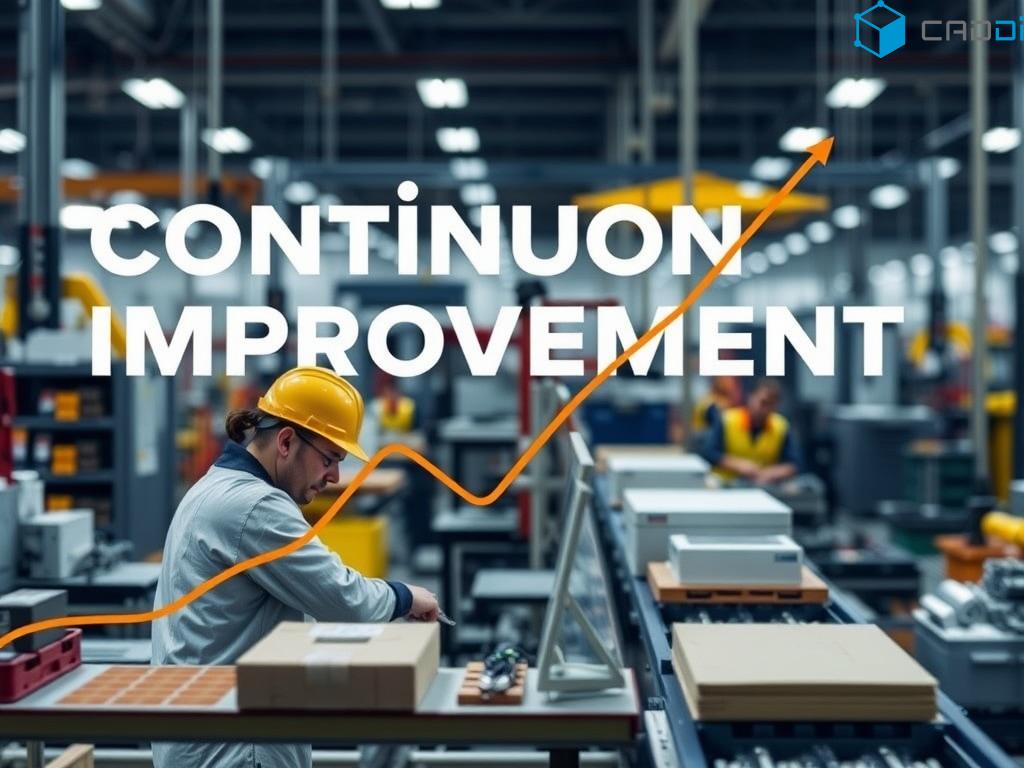
A Perpetual Pursuit of Perfection
However, this journey is not without its challenges. Organizations must overcome resistance to change, allocate resources effectively, and maintain a long-term commitment to sustaining improvements[5]. Nonetheless, the rewards of increased efficiency, reduced costs, and competitive advantage make the pursuit of continuous improvement an invaluable endeavor.
As the manufacturing landscape continues to evolve, the ability to adapt, innovate, and continuously improve will be the hallmark of successful organizations. By fostering a culture of relentless betterment, manufacturers can future-proof their operations and thrive in an ever-changing business environment.
How Organizations Master the Art of Continuous Improvement in Manufacturing
Continuous improvement in manufacturing drives operational excellence through incremental changes that enhance efficiency, quality, and productivity. It engages employees, optimizes processes through data-driven methodologies like Lean and Six Sigma, and fosters a culture of innovation to minimize waste, costs and deliver superior customer value.
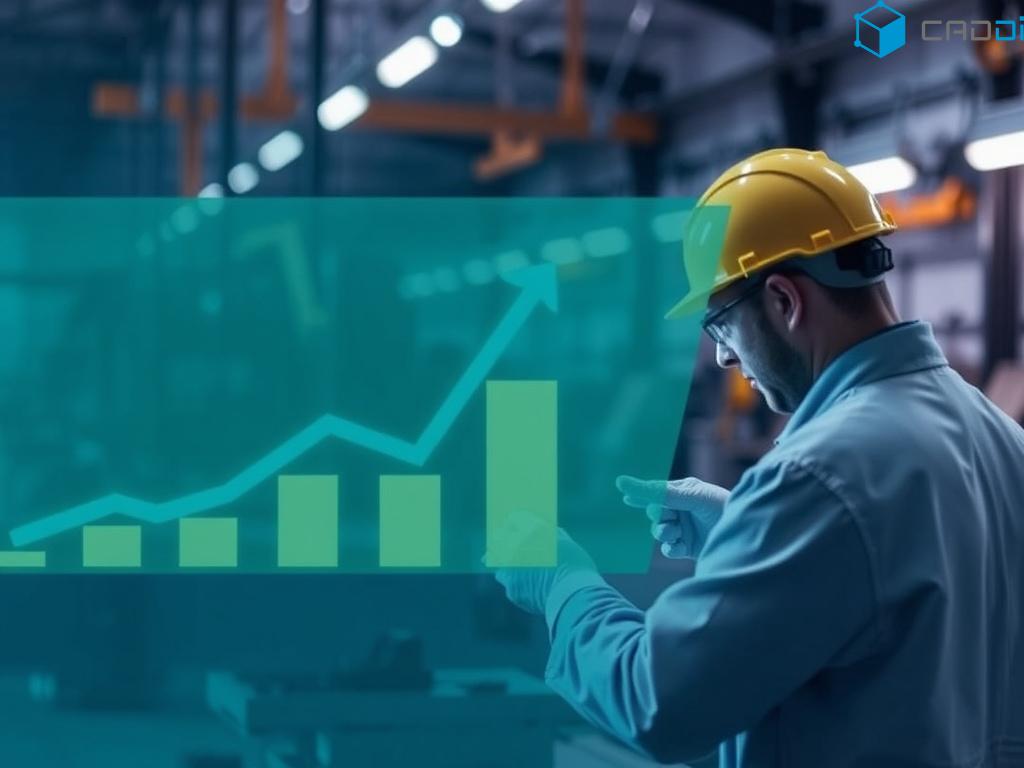
How Organizations Master the Art of Continuous Improvement in Manufacturing
Leveraging Kaizen to Transform Machine Shop Operations
Implementing best kaizen ideas is pivotal for machine shops aiming for operational excellence. The kaizen blitz approach, involving cross-functional teams identifying and rapidly executing improvement opportunities within focused areas, rejuvenates stagnant processes. A renowned machine tooling manufacturer harnessed kaizen events to minimize setup times, boosting productivity by 35%. How can your organization unlock such transformative potential?
“Kaizen emphasizes continuous, incremental improvements made by everyone, not just managers. Teams study a process, gather data to truly understand it, and work together to make targeted improvements.” – Jeffrey Liker, Author of “The Toyota Way”
Essential Tools for Sustainable Manufacturing Gains
Effective kaizen implementation necessitates a mastery of key techniques like Value Stream Mapping (VSM) to visualize material and information flows, exposing inefficiencies ripe for optimization. 5S methodology (Sort, Set in Order, Shine, Standardize, Sustain) instills operational discipline, while Poka-Yoke or mistake-proofing mechanisms prevent defects. Statistical Process Control (SPC) employs data to monitor processes, enabling proactive adjustments before issues arise. Leveraging this toolkit harmonizes workflows and embeds quality from start to finish.
Harvard Business Review spotlights DJO Global as an exemplar: “DJO took an integrated approach to lean and six sigma, using data and analysis to drive continuous improvement in quality, cost reduction, and streamlined operations.”
Cultivating an Ecosystem of Empowered Problem-Solvers
Continuous improvement transcends mere process optimization – it demands cultural transformation. Nurturing this mindset requires immersive training programs that develop problem-solving capabilities at all levels. Komatsu America, a major construction equipment manufacturer, achieved phenomenal success through its Kaizen Promotion Process. Employees collaborate in rapid improvement cycles and present solutions to leadership, fostering engagement and buy-in.
Progressive organizations recognize the pivotal role employees play in sustaining impactful change. By establishing feedback loops and celebrating wins, they reinforce the message that every voice matters. This collaborative approach accelerates organization-wide ownership of improvement initiatives, yielding compound benefits over time.
Kaizen Success Factors | Description |
---|---|
Cross-functional Collaboration | Break down silos for holistic process visibility |
Extensive Employee Training | Equip teams with problem-solving skills |
Visible Leadership Support | Reinforce organizational commitment |
Structured Execution Model | Standardize improvement cycles for consistency |
Performance Tracking | Quantify impact and refine based on insights |
Does your manufacturing strategy adequately equip teams with the skills and mindset to drive meaningful kaizen outcomes? How might emerging technologies like AI and predictive analytics augment your continuous improvement capabilities?
Bold Results from Relentless Commitment to Continuous Evolution
Achieving breakthrough performance requires an unwavering dedication to incremental gains aggregated over time. Toyota’s legendary Production System demonstrates what’s possible with sustained kaizen efforts, yielding staggering productivity gains of over 100% across quality, changeover times and inventory reductions. Ingrained habits of critically evaluating each process, questioning assumptions and iterating continuously keep Toyota innovating proactively.
Resilient organizations realize the transformative power of small, consistent steps – finding the next 1% improvement opportunity rather than chasing quantum leaps. Each process streamlined, each defect eliminated, and each employee empowered to think like an owner creates competitive differentiation.
Can your organization reimagine manufacturing as an endless cycle of calculated refinements driven by purpose-built systems? Building that capability unlocks exponential value creation through continuous improvement.
As this comprehensive exploration showcases, harnessing the principles of continuous improvement calls for much more than implementing isolated lean tools. It demands holistic transformation – an organizational renaissance where every process, every role, and every mindset aligns towards perpetual enhancement. While immensely challenging, those that master this discipline gain an enduring competitive edge through superior quality, agility and customer-centricity. The path forward lies in steadfast commitment to empowering problem-solvers, trusting data over assumptions, and embracing each day as an opportunity to elevate performance. What will your first bold stroke on this journey be?
Propelling Manufacturing Excellence: Continuous Improvement Strategies
Continuous improvement lies at the heart of operational success for manufacturers. By committing to incremental and breakthrough enhancements, organizations unlock efficient production, quality enhancement, operational excellence, cost reduction, and a powerful competitive advantage.
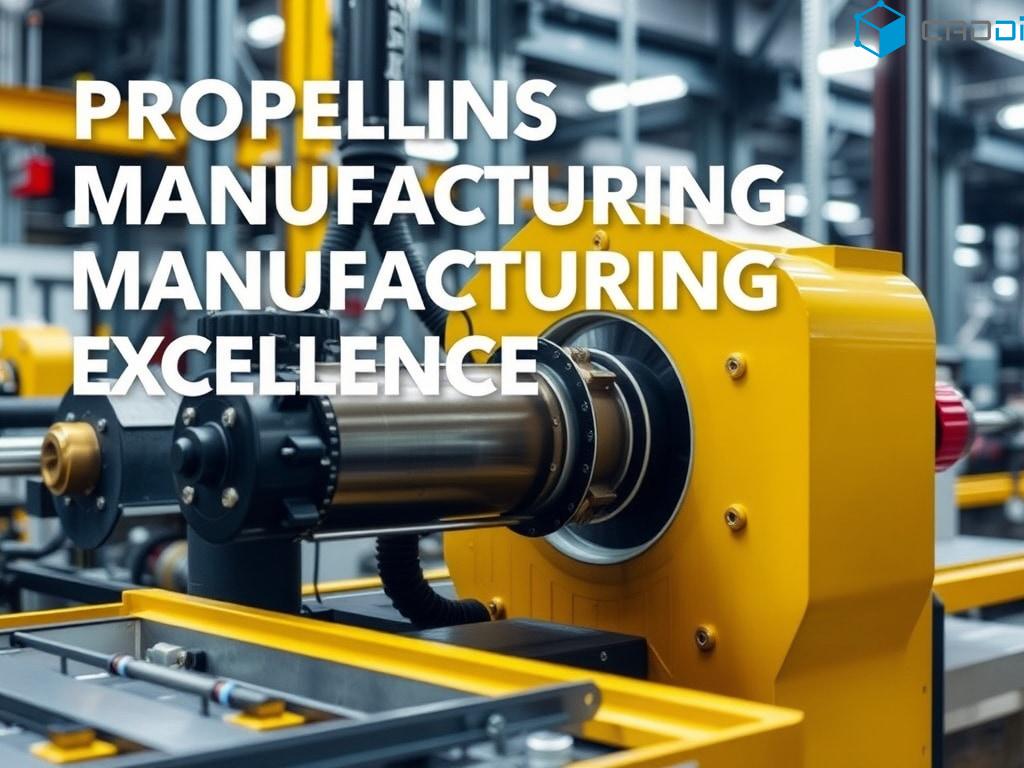
Propelling Manufacturing Excellence: Continuous Improvement Strategies
How Do Organizations Implement Best Kaizen Ideas for Machine Shops?
Leading manufacturers leverage essential tools and techniques like Lean Manufacturing, Six Sigma, and Kaizen to drive improvement. General Electric pioneered Six Sigma, saving over $1 billion annually by reducing defects and streamlining processes.
“The key is engaging frontline employees who have first-hand insights into bottlenecks and inefficiencies,” notes Jaime Kwick, Director of Continuous Improvement at 3M. Effective training equips teams to identify opportunities through techniques like value stream mapping.
A hypothetical example: A machine shop analyzes setup times, eliminating non-value-added steps and standardizing the remaining procedure. This Kaizen approach delivers 15% faster changeovers, boosting productivity.
What Drives Success in Manufacturing Continuous Improvement?
Per a PwC study, top-quartile innovators generated 5.6x more revenue from new products and services. Continuous improvement demands data-driven decision making fueled by sophisticated performance metrics.
Leadership commitment and an organizational culture fostering employee empowerment are vital. At Autoliv, the world’s largest automotive safety supplier, dedicated “Lean coaches” mentor teams in applying Lean tools for aggressive improvement goals.
But it’s not a one-time effort – continuous monitoring sustains positive change over time through regular auditing and adjustments. Toyota’s legendary manufacturing system demonstrates how systematic improvement becomes deeply ingrained.
Could manufacturers gain deeper employee buy-in by incentivizing improvement ideas? An open-ended question warranting exploration.
How Has Continuous Improvement in Manufacturing Industry Evolved?
Emerging digital technologies are transforming continuous improvement capabilities. Predictive analytics pinpoint underperforming assets, while digital twins simulate process changes before implementation.
Furthermore, global trends like growing supply chain complexity amplify the need for manufacturing agility. A table comparing traditional and digital-enabled continuous improvement approaches highlights the increasing sophistication:
Traditional | Digital-Enabled |
---|---|
Manual data collection | Real-time performance dashboards |
Periodic audits | Constant monitoring via IIoT sensors |
Offline analysis | AI-driven process optimization |
Employee surveys | Integrated voice of customer |
As forward-thinking manufacturers integrate Industry 4.0, continuous improvement will become an ever-more data-driven, automated, and connected endeavor – a relentless pursuit of enhanced competitiveness on the global stage.
Continuous Improvement in Manufacturing: Key to Operational Excellence
In today’s fast-paced manufacturing landscape, continuous improvement strategies are paramount for achieving operational excellence. This proactive approach focuses on identifying inefficiencies, implementing incremental enhancements, and measuring outcomes to drive sustainable progress. Leading organizations like Toyota and General Electric have mastered this art, fostering a culture of perpetual refinement.
What Drives Success?
Strong leadership and an organizational culture embracing change are vital catalysts. Data-driven decision-making powered by robust performance metrics enables targeted improvements. Remember, continuous improvement is an ongoing journey, not a one-time destination.
Manufacturing Evolution
The integration of digital technologies and Industry 4.0 principles has catalyzed transformative change. Real-time data analytics, automation, and connected systems unlock new frontiers in process optimization. Globally, best practices like Lean Manufacturing and Six Sigma are being adopted to enhance quality and efficiency.
Common Pitfalls
Overcoming resistance to change and maintaining momentum can be challenging. Resource constraints also hinder progress. A McKinsey study found companies failing to sustain improvements often “lacked leadership engagement or struggled with change management.”
Achieving Excellence through Innovation
Cross-industry knowledge sharing sparks novel ideas. Advanced analytics enable predictive maintenance, preempting failures. Most crucially, cultivating a learning culture empowers employees to drive continuous improvement from within.
The competitive advantages are clear: market differentiation via operational excellence, heightened customer satisfaction, and cost optimization through waste reduction. As Kaizen philosophy states, “There can be no improvement without change.” Embracing continuous improvement unlocks manufacturing’s true potential.
How does your organization foster a mindset of perpetual refinement? What untapped opportunities await? The path to excellence is paved with sustained, incremental progress.
Foster a Culture of Relentless Optimization
Empowering employees and fostering an organizational culture that embraces continuous improvement is crucial for manufacturing excellence. Richard Kunst, CEO of Continuous Improvement Associates, emphasizes, “Successful continuous improvement requires commitment from leaders to create an environment where employees feel valued and encouraged to identify problems and implement solutions.” This people-centric approach not only boosts productivity and efficiency but also enhances employee engagement and job satisfaction.

Foster a Culture of Relentless Optimization
A prime example is Harley-Davidson’s Continual Improvement Process (CIP), which encourages employees to submit improvement ideas. Over 10 years, they have implemented over 10,000 employee suggestions, resulting in significant cost savings and quality improvements[4]. How can your organization cultivate a similar culture of empowerment and continuous learning?
Data-Driven Decision Making: The North Star
In the pursuit of continuous improvement, data-driven decision making serves as the guiding compass. Key Performance Indicators (KPIs) like Overall Equipment Effectiveness (OEE), cycle time, and defect rates provide invaluable insights into process performance. Regular monitoring and analysis of these metrics against benchmarks help pinpoint areas for optimization.
The Massachusetts Institute of Technology (MIT) conducted a study[5] on the impact of data-driven decision making in manufacturing. The results revealed a 12% increase in productivity and a 19% reduction in operational costs for companies that effectively leveraged data analytics. How can you leverage real-time data and advanced analytics to drive your continuous improvement initiatives?
Agile Manufacturing: Adapting to Market Dynamics
In today’s fast-paced business landscape, agility and the ability to adapt to evolving market conditions are paramount. Continuous improvement methodologies like Lean Manufacturing and Kaizen empower organizations to swiftly respond to customer needs and mitigate disruptions.
Consider the case of Toyota’s Production System (TPS), a pioneering approach that emphasizes waste elimination and continuous improvement. By rapidly identifying and addressing inefficiencies, Toyota has consistently delivered high-quality products while maintaining a competitive edge[3]. What processes can you streamline to enhance your organization’s responsiveness and flexibility?
Digital Transformation: The Catalyst for Innovation
The integration of digital technologies has emerged as a powerful catalyst for continuous improvement in manufacturing. Solutions like machine monitoring, predictive analytics, and real-time data enable organizations to uncover hidden inefficiencies and optimize processes.
According to PTC, a leading industrial software company, “Digital manufacturing solutions can increase efficiency by up to 20% and provide real-time performance data, enabling continuous improvement.”[2] Imagine the potential impact of leveraging cutting-edge technologies to drive innovation and operational excellence within your organization.
Industry 4.0: The Future of Continuous Improvement
The future of continuous improvement in manufacturing is intrinsically tied to the Industry 4.0 revolution. Emerging technologies like advanced analytics, predictive maintenance, and the Internet of Things (IoT) are poised to revolutionize the way we approach process optimization.
As stated by Deloitte, “Industry 4.0 technologies enable real-time data collection, analysis, and decision-making, allowing manufacturers to continuously improve processes and respond rapidly to changing market demands.”[6] How can you leverage these cutting-edge innovations to stay ahead of the curve and maintain a competitive edge?
In the ever-evolving manufacturing landscape, continuous improvement is not an option but a necessity. By embracing a culture of relentless optimization, data-driven decision making, agile methodologies, and digital transformation, organizations can achieve operational excellence, drive innovation, and deliver superior value to customers. The future belongs to those who consistently challenge the status quo and strive for constant reinvention.
FAQ: Continuously Optimizing Manufacturing Operations
How can organizations foster a culture conducive to continuous improvement?
Cultivating an organizational culture that embraces continuous improvement begins with strong leadership commitment. Empower employees by providing training on problem-solving techniques, encouraging idea sharing, and recognizing improvement efforts. Establish open communication channels and feedback loops to ensure that all voices are heard. Celebrate successes, both small and significant, to reinforce the value of continuous learning and refinement.
What role does data play in driving continuous improvement initiatives?
Data-driven decision-making is the cornerstone of effective continuous improvement strategies. Identify and monitor relevant Key Performance Indicators (KPIs) to gain insights into process performance. Leverage real-time data from sensors, analytics tools, and digital platforms to pinpoint areas for optimization. Continuously analyze and interpret this data to make informed decisions and track the impact of implemented improvements.
How can manufacturers balance continuous improvement efforts with responsiveness to market demands?
Agile manufacturing methodologies, such as Lean and Kaizen, enable organizations to adapt swiftly to evolving market conditions while maintaining a focus on continuous improvement. These approaches emphasize waste elimination, streamlined processes, and rapid identification and resolution of inefficiencies. By fostering a culture of flexibility and constant refinement, manufacturers can simultaneously enhance operational excellence and meet customer needs.
What is the role of emerging technologies in continuous improvement?
Industry 4.0 technologies, including advanced analytics, predictive maintenance, and the Internet of Things (IoT), are revolutionizing continuous improvement in manufacturing. These cutting-edge solutions enable real-time data collection, analysis, and decision-making, allowing manufacturers to continuously optimize processes and respond rapidly to changing market demands. Embracing digital transformation empowers organizations to unlock new frontiers of operational excellence and innovation.
As the manufacturing landscape continues to evolve, embracing a mindset of perpetual optimization and leveraging the power of data, agility, and emerging technologies will be crucial for sustained success.